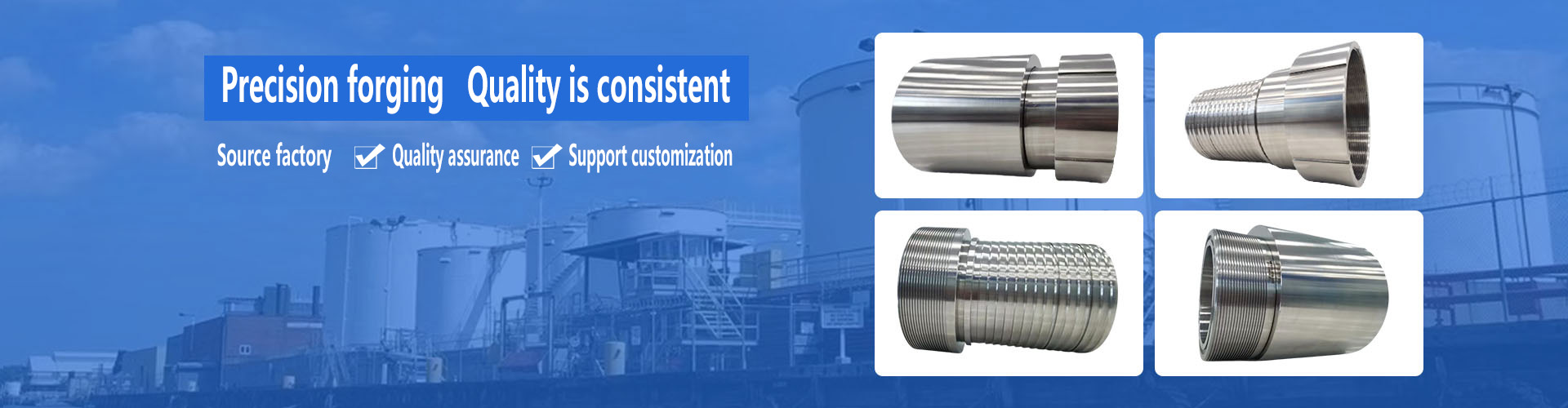
Titanium alloy rolling technology is an important metal processing technique that involves forming titanium alloy materials into the desired shape and size through rolling.
Key points of process
The rolling process of titanium is a key step in the production of titanium alloys, which directly affects the microstructure and macroscopic properties of the material. Here are some key points of titanium alloy rolling process:
1. Rolling temperature control:
The rolling temperature window of titanium alloy is narrow and its thermal conductivity is poor, so temperature control of the slab is crucial. Excessive opening temperature or rolling deformation may cause a sharp increase in temperature in the central area of the rolled piece, resulting in poor plasticity and uneven rolling.
2. Multi pass rolling:
The rolling of titanium alloy plates usually requires multiple passes of hot rolling, which is suitable for controlling the microstructure and properties of the material. Annealing treatment may be required between each pass to restore the plasticity of the material.
By gradually reducing the thickness of the material through multiple rolling passes,
3. Reduction rate allocation:
The distribution of reduction rate has a significant impact on the anisotropy of the material during the rolling process. For example, when the reduction ratio of horizontal and vertical rolling passes is distributed at 1:1, the anisotropy of the material is basically eliminated.
4. Rolling speed:
The rolling speed will affect the temperature distribution of the slab, thereby affecting the rolling quality and production efficiency. In the rolling stage, to prevent accidents caused by biting, low speed is generally used; As the rolled piece becomes thinner, the rolling speed can be increased, but usually not exceeding a certain value.
5. Rolling equipment:
The use of advanced rolling equipment, such as fast transverse reversible units, continuous rolling units, precision rolling mills, and modular rolling mills, can improve rolling efficiency and product quality.
6. Automated control system
Develop a fully automated control system for the entire process, achieve temperature control and rolling automation production, and improve the automation and intelligence level of the production process.
7. New Rolling Process
Using a three roll Y-shaped rolling mill instead of a traditional two roll rolling mill can achieve single line twist free micro tension rolling and improve rolling speed.
8. Rolling window determination:
Determine the rolling temperature window for hot-rolled titanium alloys through experiments and simulation analysis, providing a basis for developing hot rolling process specifications.
9. Preparation of raw materials:
Pure titanium and low-alloy compound gold plates can be supplied in the form of forging, rolling or flat ingots, while high alloy compound gold plates require free forging.
10. Rolling procedure formulation:
The formulation of rolling regulations includes aspects such as billet design, reduction system, speed system, temperature system, etc., which require comprehensive consideration of material characteristics, equipment capacity, and production efficiency.
Technical features
1. Hot Rolling:
Hot rolling is a rolling process carried out above the recrystallization temperature of metal materials, which can significantly reduce the deformation resistance of materials and improve rolling efficiency.
Suitable for the production of large-sized titanium alloy sheets and rods.
2. Cold Rolling:
Cold rolling is a rolling process carried out at room temperature, which can improve the surface quality and dimensional accuracy of materials, but requires high plasticity of materials.
Usually used for producing high-precision thin plates and strips.
3. Reversible Rolling:
Reversible rolling refers to the process in which the rolled material passes through the rolling mill multiple times, and the direction of the rolled material is changed after each pass to improve its anisotropy.
4. Near isothermal rolling:
An innovative rolling concept that achieves near constant temperature rolling of titanium alloys by controlling deformation amount, deformation speed, and rolling cycle, improving rolling efficiency and material properties.
5. Unconventional passes and flexible rolling:
Allow the use of different rolling passes and rolling systems to adapt to different material characteristics and production needs.
6. New efficient rolling mode of "one fire to produce materials":
Through innovative rolling concepts and processes, efficient production of aviation grade titanium alloys has been achieved, increasing the weight of small-sized wire coils.
7. Large specification BDM850 fast transverse reversible rolling mill:
A type of equipment designed for rolling large section titanium alloys, capable of achieving short pass intervals and high efficiency rolling.
8. Stepper rolling mill, spiral rolling mill, Y-shaped rolling mill, planetary rolling mill:
Rolling equipment has its own characteristics and is suitable for the production of different specifications of bars.
The development of titanium alloy rolling technology continuously promotes the progress of material processing technology. By improving the rolling process and equipment, the comprehensive performance of titanium alloy materials can be enhanced to meet the demands of the high-end market.